From Chaos to Control: How To Optimize Your Construction Fleet Tracking
Construction fleet tracking is a vital component of efficient project management and resource allocation in the construction industry. By implementing an effective construction fleet tracking system, construction professionals can streamline operations, maximize productivity, and gain greater control over their fleet management processes.
Here, we will explore the importance of construction fleet tracking and provide practical guidance on how to optimize its usage, including integrating AtoB's fuel cards to enhance fuel cost management and overall fleet performance.
Understanding the Importance of Construction Fleet Tracking
Construction fleet tracking plays a crucial role in streamlining operations and maximizing productivity in the construction industry—and the investment pays off. According to a 2021 report by G2, 32% of GPS tracking users reported a positive ROI in less than 6 months 1. By accurately tracking the location and movement of construction equipment and vehicles, project managers can efficiently allocate resources, identify potential bottlenecks, and ensure timely project completion.
Furthermore, construction fleet tracking enhances project management by providing real-time visibility into the progress of tasks, enabling quick adjustments and mitigating potential delays. The use of construction fleet tracking systems can result in substantial cost savings and operational efficiency improvements, making it an indispensable tool for construction professionals.
Choosing the Right Construction Fleet Tracking System
When selecting a construction fleet tracking system, it is essential to consider key factors that align with the specific needs of your construction company.
- Scalability is crucial, as it allows for future expansion and accommodates the growth of your fleet operation.
- Real-time tracking capabilities provide accurate and up-to-date information regarding equipment location and asset utilization, enabling prompt decision-making.
- Reporting capabilities offer valuable insights into fleet performance, fuel consumption, and vehicle maintenance requirements.
- Integration options with other software solutions, such as project management tools, can streamline workflows and enhance overall efficiency.
Setting Up Your Construction Fleet Tracking System
To effectively set up a construction fleet tracking system, follow these step-by-step instructions:
- Install the necessary hardware, such as GPS trackers, on each vehicle and construction equipment.
- Configure the software to ensure seamless data collection and accurate reporting.
- Integrate the tracking system with other relevant software and project management tools.
- Train your team on how to use the construction fleet management platform effectively, emphasizing data accuracy and responsible usage.
By following these best practices, you can optimize the functionality of your construction fleet tracking system and ensure accurate data collection for enhanced decision-making.
Best Practices for Utilizing Construction Fleet Tracking Data
Construction fleet tracking systems collect various types of data, including vehicle locations, fuel consumption, and driver behavior. Interpreting and analyzing this data can unlock valuable insights and performance metrics for your construction company.
By leveraging fleet tracking data, construction professionals can identify areas for improvement, optimize fuel consumption, and minimize vehicle maintenance costs. For example, tracking data may reveal inefficient routes or excessive idling, enabling you to take corrective actions and reduce fuel expenses.
By utilizing construction fleet tracking data effectively, you can drive operational improvements, improve safety, and enhance overall fleet performance.
{{CTA}}
Maximizing Efficiency through Real-Time Fleet Monitoring
Real-time fleet monitoring empowers construction professionals with up-to-the-minute information on vehicle locations, statuses, and driver activities. By harnessing real-time data, project managers can make proactive decisions, optimize resource allocation, and respond promptly to unforeseen circumstances. For instance, if a project site requires additional equipment, real-time fleet monitoring can identify the nearest available vehicle and expedite its deployment, saving time and reducing downtime.
Additionally, by using a fleet fuel card from AtoB, you gain custom control and can instantly enable or disable cards, whitelist or blacklist merchants, and set limits on how much can be spent and when cards can be used—all in a couple of clicks. To maximize efficiency, construction professionals should prioritize the integration of real-time fleet monitoring into their construction fleet tracking strategy.
Enhancing Safety with Construction Fleet Tracking
Safety is a paramount concern in the construction industry, and construction fleet tracking plays a vital role in improving safety standards. In fact, 42% of fleet managers reported considerably fewer safety incidents since using fleet tracking software to monitor driver behavior.
Features such as geofencing allow project managers to define restricted areas and receive alerts if a fleet vehicle enters or exits these zones. Driver behavior monitoring enables the identification of risky driving habits, encouraging safe driving practices and reducing accidents. Furthermore, construction fleet tracking systems provide emergency response capabilities, ensuring swift action in the event of an incident.
By leveraging construction fleet tracking—including the use of a fuel card that blocks transactions that occur outside of a vehicle's vicinity or exceed its tank capacity—construction professionals can create a safer work environment for their teams and mitigate potential risks.
Improving Communication and Coordination with Fleet Tracking
Construction fleet tracking facilitates effective communication and coordination between drivers, dispatchers, and project managers. Messaging systems integrated into fleet tracking software enable seamless communication and provide essential updates regarding project progress, route changes, and delivery schedules.
GPS tracking enhances coordination by enabling project managers to monitor the real-time location of vehicles and make informed decisions based on their proximity to specific project sites.
Additionally, route optimization features help reduce fuel consumption and improve overall efficiency. Taking advantage of a fuel card is yet another way to promote transparency and enhance security across your fleet. By leveraging construction fleet tracking's communication and coordination capabilities, construction professionals can streamline workflows and enhance collaboration.
Overcoming Challenges in Implementing Construction Fleet Tracking
Implementing a construction fleet tracking system may face challenges and resistance from employees. To overcome these obstacles, it is crucial to emphasize the benefits of fleet tracking and involve employees in the decision-making process.
Clear communication and training sessions can help employees understand the purpose and advantages of fleet tracking and address any concerns. Managing change effectively and encouraging employee buy-in are essential for successful implementation.
By taking these steps, construction professionals can navigate the challenges and ensure a smooth transition to a construction fleet tracking system.
Analyzing and Utilizing Construction Fleet Tracking Reports
Analyzing tracking reports is key to gaining insights into fleet performance and identifying areas for improvement. Construction fleet tracking systems generate various reports, including fuel consumption, maintenance scheduling, and driver productivity. By interpreting these reports, construction professionals can make data-driven decisions, optimize resource allocation, and enhance operational efficiency. For example, identifying vehicles with high maintenance costs allows for proactive maintenance scheduling, reducing downtime and minimizing expenses.
Utilizing construction fleet tracking reports effectively empowers construction professionals to make informed decisions and maximize fleet performance.
Measuring Success: Key Performance Indicators for Fleet Tracking
Measuring success in construction fleet tracking involves tracking key performance indicators (KPIs) relevant to your fleet's performance. KPIs may include construction fleet management operating costs, fuel consumption per vehicle, driver productivity, and overall fleet efficiency. By monitoring these KPIs over time, construction professionals can evaluate the effectiveness of their fleet tracking system and identify areas that require improvement.
For instance, a decrease in fuel consumption per mile can indicate the successful implementation of fuel-saving strategies. By measuring the right KPIs, construction professionals can gauge the success of their fleet tracking efforts and drive continuous improvement.
Fueling the Future: The Synergy of AtoB's Fuel Cards and Construction Fleet Tracking
AtoB's fuel cards offer a valuable synergy when integrated into construction fleet tracking systems. By incorporating fuel cards, construction professionals can effectively manage fuel costs, mitigate the chances of construction fraud, and gain control over fuel consumption.
AtoB's fuel cards provide access to fuel discounts, detailed fuel purchase reports, and spending controls, allowing for optimized fuel cost management. By integrating our fuel cards with construction fleet tracking, construction professionals can enhance their overall fleet performance, minimize fuel expenses, and achieve greater control over their operations on a daily basis.
Embrace the Power of Construction Fleet Tracking and Fuel Efficiency
Optimizing construction fleet tracking is crucial for construction professionals aiming to streamline operations, maximize productivity, and enhance project management.
By choosing the right asset tracking system, setting it up effectively, utilizing real-time data, enhancing safety measures, improving communication and coordination, overcoming implementation challenges, analyzing tracking reports, and measuring key performance indicators, construction professionals can achieve greater control over their fleet management processes.
Furthermore, integrating AtoB's fuel cards into construction fleet tracking strategies enhances fuel cost management and overall fleet performance. Take action today to optimize your construction fleet tracking and experience the transformation from chaos to control!
And, if you’re interested in learning more about how fleet management helps the construction industry, be sure to check out our blog!
Sources:
1 Nair, Sujith. “45 Fleet Management Statistics to Help Reduce Operational Costs,” 18 June 2021, www.g2.com/articles/fleet-management-statistics.
Get started with AtoB
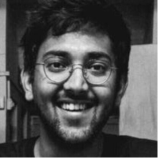
Reviewed by
Vedant Khamesra is the driving force behind product management at AtoB. Specializing in strategic partnerships, SMB solutions, and new product development, Vedant seamlessly navigates P&L responsibilities while leading product execution and strategy. He is fueled by AtoB's mission to empower truckers and fleets with intelligent financial tools and services, making their lives easier and more rewarding.
Start saving today
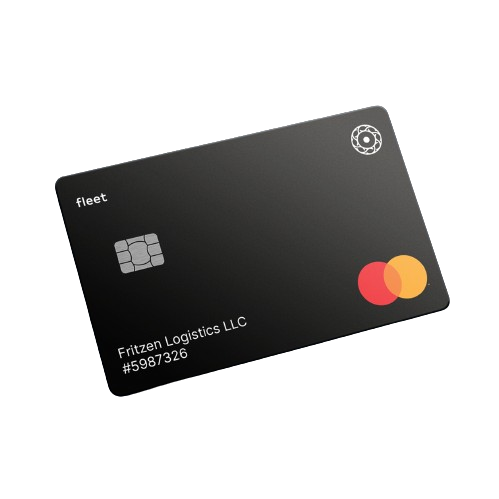