Manage Your Delivery of Construction Materials
Construction projects have dozens of moving parts. Successfully juggling all of these concerns is made all the more difficult by tight timelines, restricted budgets, and our current supply chain crunch.
Despite the challenges of construction fleet management, project managers do their best work when work disruptions are at a minimum. The last thing they want to occur is to have the workers, heavy-duty machines, and equipment on-site and ready to go, only to have the day’s work paused due to delayed construction materials delivery. These work disruptions are easily avoidable with proper planning and foresight—and a little help from reliable construction material delivery to ensure that materials are delivered on time and safely.
Do you run such a construction company or plan to enter the industry?
This guide is for you.
Construction Materials and Planning
For any project, there may be thousands of different building materials that go into constructing a bridge, building, or piece of infrastructure. Instead, the project manager and contractors must carefully research and make sourcing decisions about the following questions:
- What materials will they need?
- Who will they source the materials from?
- How much of each material do they need?
- When will the materials be used within the project timeline?
- Where will materials be stored when not in use?
- Will they be bought all at once or ordered piecemeal as the project progresses?
If they want the project to move as efficiently as possible, the right supplies and equipment need to arrive undamaged and on time. And since these materials tend to be used in a complementary fashion, even a single missing component could disrupt the day’s workflow.
The Role of a Construction Materials Delivery Company
Such significant logistical constraints demonstrate the importance of delivery freight contractors. As a partner with the construction project manager, you’re tasked with coordinating schedules and then transporting the necessary materials according to the planned timeline.
The work process can vary significantly from company to company but typically breaks down into two main business model categories:
- Just-in-time – Some construction material delivery startups may only handle smaller orders for last-minute, “just-in-time” orders. In such cases, they’ll typically have drivers that act as independent contractors and operate a van or pickup trucks.
- Heavy haul – In other instances, freight companies may be heavy haul specialists with a fleet of larger trucks and transport vehicles necessary to move specialty construction equipment, hazardous materials, bulky materials, or oversized machinery.
For either business model, the delivery of construction materials can benefit construction managers in several different ways:
- Reliable scheduling (both) – Project delays can be costly. Construction managers can plan workers’ schedules and project workflows confidently knowing that materials will arrive as expected.
- Transparency (both) – Modern delivery companies provide technologies that allow construction managers to track the progress of shipments in real time, providing the most accurate picture of when deliveries will be arriving.
- Streamline inventory (just-in-time) – With last-minute ordering, construction managers can order supplies or fill in materials on an as-needed basis. This saves them money that might otherwise have to be spent on securely storing materials that won’t be immediately used.
- Specialty delivery (heavy haul) – Are there bulky pieces of equipment that need to go to the job site? Are there materials that require extra protection to ensure that they arrive in one piece? Heavy haul companies offer the expertise and equipment necessary to deliver large, hazardous, or bulky items.
Delivery Logistics Business Model
What are the main facets of the job?
For a freight delivery company, you are expected to ensure that the construction project has the right materials on hand when they need them. Supporting construction managers is practically impossible without a comprehensive materials delivery logistical plan that covers several different concerns about your job:
Inbound Delivery
Your primary task is to bring products, equipment, and possibly even machinery to the job site, in the proper amount, in working order, and on time. Both early and late deliveries could cause headaches that impact the construction project and leave the client unsatisfied with your services.
Outbound Delivery
Quite often, there will be excess materials that need to be returned or sent back to storage. Waste and debris need to be removed from the site and properly disposed of. Also, rented equipment or machinery will need to be sent back to their owner to avoid late fees. You may be asked to pick up and transport those materials to warehouses, businesses, and other off-site locations.
Equipment and Material Transportation Logistics
Different construction materials need to arrive at different points within the project. You need to work closely with the project manager to understand timelines and make detailed delivery plans ahead of time.
Particularly for heavy-haul companies, many types of materials, equipment, or machinery may require you to use special transportation vehicles. For instance, heavy and bulky materials such as roofing materials may need to be transported via open deck vehicles or bulk materials may require special trailers.
If you don’t own those trucks, but agree to move those materials, you’ll need to rent or lease machinery to move the components.
Offloading and Site Management
Will you be offloading the materials? Who will be in charge of confirming that the delivery was done on time, in good condition, and as ordered?
There needs to be a proper chain of custody over the materials so that once they’re off the truck, they’re no longer your responsibility.
Regulatory Compliance
For delivery logistics, a major factor that must be prioritized is safety—for drivers, pedestrians, and other motorists. There are a variety of compliance regulations that govern freight industry operations and which you must abide by. Materials need to be safely and securely transported and delivered so as to avoid injuries, fatalities, and the possibility of costly liability suits.
{{CTA}}
Construction Material Delivery Management Challenges
There are several significant management challenges that practically any construction material delivery company will face. These include:
Fleet Acquisition
To operate as a delivery company, you’ll need vehicles to transport the materials in the first place.
Will you own your vehicles or lease them? Does your business model require that your contracted drivers use their own vehicles? If you do purchase, will you buy new or used?
Questions such as these are crucial for startups seeking to enter the space. Whether the vehicle is bought, leased, or contracted through the driver, in any case, this will likely represent a significant portion of your capital allocation.
Routing Optimization and Scheduling
Since there are different types of construction trucks, you’ll want to choose one that can handle constant delivery. Your business model depends on speedy delivery service. Therefore, drivers—especially if they’re going longer distances—need to be taking the most efficient and cost-effective route possible.
There may be several elements to consider, including:
- Traffic
- Distance
- Timeline
- Road conditions
- Street limitations
- Site restrictions
- Truck capacity
Proper route optimization and planning minimize the chances of failed or delayed deliveries. It also can reduce the costs of gas and maintenance.
Preventative Vehicle Maintenance
If you own your fleet of delivery vehicles, you must ensure that they’re in good working order. To accomplish that, regular inspection, maintenance, and repair via preventive vehicle maintenance is necessary.
Performing routine inspection and repair saves you money in the long run by addressing small issues before they can transform into larger ones. It also empowers you to:
- Protect drivers, motorists, and pedestrians
- Optimize vehicle performance
- Lower operational costs
- Increase vehicle resale value
Learn more about the best fleet maintenance tips to ensure your vehicles are in tip-top shape.
Fleet Expenses
To run a successful business, you need to have visibility and control over your spending and cash flow. Doing so enables you to take on more clients, set budgets, invest in equipment or employees, and grow the business.
To identify opportunities for cost-savings, you need to know where and how you’re spending your money.
For example, fuel is likely your largest operating fleet expense on your ledger, especially now that both gas and diesel are at or near historic highs.
Are you looking for ways to reduce fuel cost expenses? You can do that by:
- Using a fuel card that provides discounts and helps you track expenses
- Tracking vehicle mileage
- Reducing idling time
- Changing driver behavior
- Optimizing routing
Delivery Documentation
As mentioned, it’s important to have documentation that confirms you did your job as contracted. Quite often, this will be a Bill of Lading (BOL)—a legal document that acts as the shipping receipt that details various factors, including:
- The type of materials
- The number of materials
- The condition of materials
- The destination for the materials
Once your driver reaches the construction site, the authorized on-site representative must sign the bill so that there’s a clear chain of custody.
AtoB—Supporting Your Delivery Business
Whether you’re an on-demand construction materials delivery startup or an established heavy haul freight business, you serve an essential support role for the construction industry.
But to last in such a high-pressure, competitive business environment, you must do everything possible to reduce your operational expenses.
That’s where we can help you start saving immediately. At AtoB, our fleet fuel cards were designed to support businesses such as yours. These cards are universally accepted, provide exclusive fuel discounts, and even provide a portal so that you can monitor and analyze your spend.
Interested in learning more about how we help power small, growing, and nationwide fleets?
Reach out today!
Sources:
US Compliance Services. Compliance Laws You Should Know.
https://www.uscomplianceservices.org/laws-and-regulations/
EIA. Weekly Retail Gasoline and Diesel Prices.
https://www.eia.gov/dnav/pet/PET_PRI_GND_DCUS_NUS_W.htm
Get started with AtoB
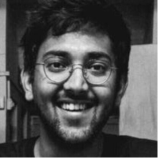
Reviewed by
Vedant Khamesra is the driving force behind product management at AtoB. Specializing in strategic partnerships, SMB solutions, and new product development, Vedant seamlessly navigates P&L responsibilities while leading product execution and strategy. He is fueled by AtoB's mission to empower truckers and fleets with intelligent financial tools and services, making their lives easier and more rewarding.
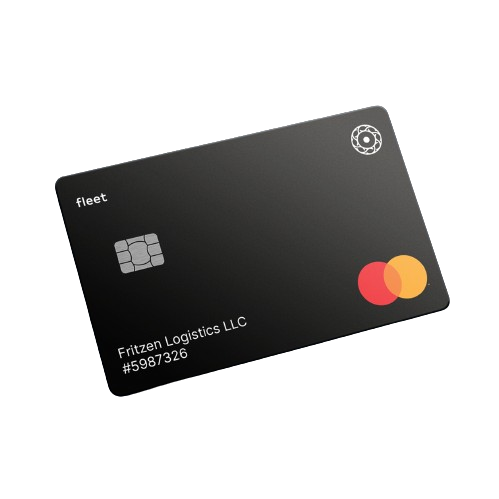